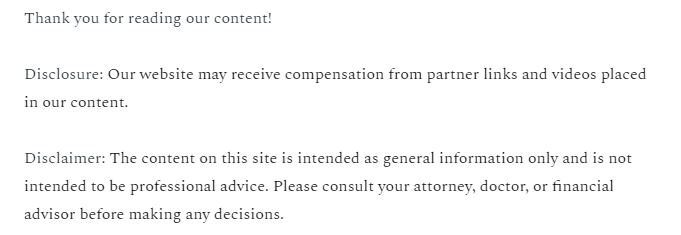
Knowing the parts of a plastic injection molding machine allows the user to avoid or minimize simple errors in operation. In general, the more machine parts to the plastics injection molding, the more potential for something to go wrong. The possibility of a problem is unique to each piece. For example, the issues that might arise with hot runner systems is different than those for cold runner systems.
What Parts Should the Operator Be Familiar With On an Injection Molding Machine?
There are three types of injection molding machine: hydraulic, mechanical, and electric. Mechanical machines require a heavy clamp during the injection molding process, making them unfavorable for precise work. Hydraulic machines are the most often used, however lack the precision of an electric machine.
Why is the hydraulic the most popular? Until 1983, it was the only option available. Also, while the electric injection molding machine is more reliable and accurate over the long term, it is also a more expensive machine.
Each machine has at least six parts divided between the injection molding component and the clamping unit. The injection molding unit has:
-
1. Heaters and Ring Plunger
2. Reciprocating crew and barrel
3. Screw motor drive
The clamping unit has the following parts:
-
1. Clamping motor drive
2. Mold
3. Tie bars
What Are the Problems That Can Occur During Operation?
The problems that show up most often with injection molding are usually attributed to an error during the molding process. Some of the common types include:
-
1. Vacuum Voids. These are air pockets that show up when the clamping pressure is inadequate during the molding process.
2. Flow Lines. These streaks occur when the cooling plastic “flows” slightly into the valve gating as the injection molding process is finishing.
3. Sink Marks. These are pits or depressions that show up when the exterior of the molded piece sets more slowly than the rest, creating a sunken appearance when it’s removed from the machine.
4. Short Shot. This is when a piece is incomplete because the mold was inadequately filled by the cold or hot runner nozzle.
5. Jetting. This shows up as a squiggly line on the surface of the product. It differs from flow lines because it is caused by the injection nozzle being too forceful with the first dose.
How Can These Common Problems Be Fixed?
Problems with an injection molding machine usually have a simple fix. For example, fixing a short shot is a matter of making it easier for the plastic to flow. This might mean choosing a different material, or by increasing the temperature of the hot runner nozzle. Hot runner nozzles are sometimes favored over cold runner nozzles for being completely sealed, which is helpful in avoiding other issues such as jetting.
Problems with an injection molding machine leave clear evidence. Often, these problems are simple to fix by making an adjustment to the mold or to the alignment of the machine.