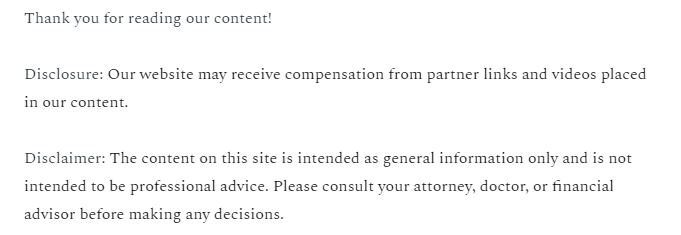
Crane systems are integral to a wide range of industries, including construction, manufacturing, shipping, and logistics. These systems allow for the lifting, lowering, and movement of heavy loads with precision and efficiency. Whether used in a warehouse to move materials or on a construction site to lift large machinery, crane systems are essential for many operations that require the handling of heavy or bulky items. Understanding the basics of crane systems, including their components, types, and uses, is key for ensuring they are used safely and effectively.
At the core of any crane system is its mechanical structure, which typically includes the crane’s frame, lifting mechanisms, and supporting components. The crane’s frame, which provides structural support, must be designed to handle the weight of the load and withstand the stresses it will experience during lifting. The lifting mechanism is responsible for raising and lowering the load and is usually composed of a hoist, chains, ropes, or cables. A well-designed frame and lifting mechanism ensure that the crane system can safely lift and move materials without failure or instability.
Hoisting mechanisms are a crucial part of crane systems. A hoist is the device responsible for raising and lowering a load, and it usually consists of a motor, drum, and lifting chain or cable. Depending on the crane system, hoists can be powered manually, electrically, or hydraulically. For example, an electric hoist is commonly used in industrial settings where heavy lifting tasks are frequent, while manual hoists are more common in smaller-scale operations or areas with limited access to electricity. The hoist is connected to a hook or other load-handling device that securely attaches to the load being lifted.
Cranes also include a trolley and bridge system in some configurations, especially for overhead cranes used in factories or warehouses. The trolley is a movable part of the crane that carries the hoist along the length of the crane’s beam, or bridge. The bridge itself spans the area where the load will be lifted, and it moves horizontally to position the load in the right place. This configuration allows the crane to cover a large area, lifting and transporting items across different parts of the workspace.
Another important component of crane systems is the control system. The control system allows the crane operator to manage the crane’s movements with precision. It includes the electrical or hydraulic controls, as well as safety mechanisms such as limit switches, emergency stop buttons, and overload protection. These controls help ensure that the crane operates within its rated capacity, preventing accidents or damage. The operator must be trained to use the control system correctly to avoid errors during operation, as malfunctioning controls can lead to serious accidents.
Types of crane systems vary depending on the specific needs of the work environment. Some of the most common types include overhead cranes, gantry cranes, and tower cranes. Overhead cranes, often used in industrial environments, consist of a bridge that moves along fixed rails to lift and move loads across a workspace. Gantry cranes, which are similar to overhead cranes, are used for lifting large items but are typically mobile and used outdoors, such as on construction sites or shipping yards. Tower cranes, commonly seen in construction, are large cranes with a fixed vertical mast and rotating jib used to lift materials to great heights.
Safety features in crane systems are critical to ensuring that operations are carried out without incidents. Safety features often include load sensors, which prevent the crane from lifting more than it can handle, as well as emergency braking systems to stop the crane in case of malfunction. Anti-collision devices are also used in areas where multiple cranes are in operation to avoid accidents. Crane systems are also equipped with limit switches to prevent excessive movement in certain directions, ensuring the crane doesn’t overextend and cause damage to itself or the environment.
Proper maintenance is key to ensuring crane systems continue to operate smoothly and safely. Regular inspections should be conducted to check for wear and tear in the hoist, cables, and other key components. Lubrication of moving parts helps prevent friction that could lead to premature breakdowns, and any signs of damage, such as frayed ropes or cracks in the structure, should be addressed immediately. Maintenance helps identify issues before they escalate, reducing the risk of operational downtime and costly repairs.
In conclusion, crane systems are indispensable tools that facilitate the lifting and movement of heavy materials in various industries. Understanding the key components—such as hoisting mechanisms, trolleys, control systems, and safety features—helps ensure that these systems are used effectively and safely. Whether using overhead cranes in a warehouse or tower cranes on a construction site, crane systems offer the flexibility and strength necessary to handle large loads. Proper maintenance and regular inspections are essential for ensuring that crane systems operate efficiently and safely, reducing the risk of accidents and extending the life of the equipment.
.