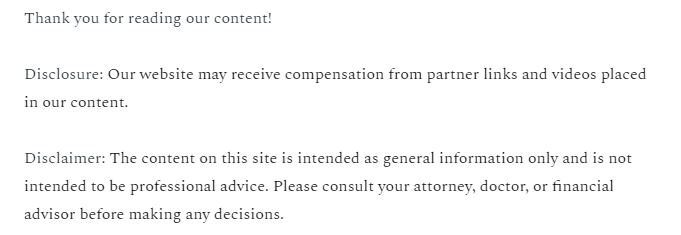

Safety in construction is one of the most important parts of the job. Without it everyday workers are put at risk for injury, the integrity of the project has an increased chance of failure and a lot of money is tossed into the garbage. Shoring and propping equipment has seen some pretty significant changes as a result, with companies attempting to find the happiest balance between natural limits in scaffolding and ways to save time and effort when piecing together a repair job or a new foundation.
Did You Know?
Before we go into the ins and outs of shoring and propping equipment let’s take a look at why it’s needed. A stunning two hundred million trips are taken every single day across deficient bridges across the nation’s 102 largest metropolitan regions, meaning these bridges are constantly getting weaker and weaker as we speak. One in nine of the nation’s bridges are rated as structurally deficient and the average age of the country’s over 600,000 bridges is 42 years old. As you can imagine, a lot of work needs to be done. But how?
Basic Safety Tips
OSHA (short for occupational safety and hazard administration) is an overseer for ensuring all construction projects, repair jobs and check-ups are done in accordance with constantly shifting and improving safety standards. OSHA requires both safe access as well as egress to all excavations, that of which includes ladders, steps and ramps, so employees can properly work in trench excavations four feet or deeper. These should also be located within 25 feet. OSHA defines any and all excavations as any man-made cut, cavity or trench in the earth’s surface.
Common Environmental Hazards
There are multiple environmental hazards to be aware of when choosing and using the right shoring and propping equipment. It’s important to test for atmospheric hazards, such as low oxygen levels or the presence of toxic gases, when cutting more than four feet deep into the earth. All excavated soil and additional materials should be kept at least two feet away from trench edges to keep equipment from tipping or outright falling into excavations. A survey provided by the Asphalt Pavement Alliance saw eight out of 10 drivers much preferring road construction to be conducted in off-hours or at night.
Shoring And Propping Necessities
Shoring and propping equipment comes in enough varieties to tackle all sorts of problems. The two types of shoring are timber and aluminum hydraulic, though these are not the only means of classification. Shoring is also classified into three classes on the basis of their supporting characteristics — you have the raking or inclined shores, the flying or horizontal shores and the dead or vertical shores. The two basic types of benching are also simple and multiple, with the type of soil determining the tools used. This can be a trench box shield, a powerbrace or a temporary bridge construction.
Creating Safer, Longer Lasting Bridges For Everyone
The world is always on the move. People aren’t about to stop driving or biking across bridges any time soon, so it’s up to construction workers to constantly repair these small to major errors in order to keep everyone safe. Working with soil means being intimately familiar with all the different shapes it can take. Type A soils are cohesive soils with a compressive strength of one and a half tons per square foot, often referred to as silty clay, sandy clay or clay loam. Type B soils are sometimes called angular gravel or silt loam, while type C soils are referred to as loamy sand, submerged soil or gravel. Shoring and propping equipment does best with a good foundation to back it up. Just like a bridge!
Good references here.