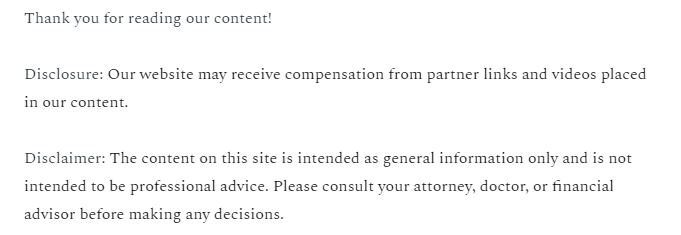
All sorts of machines and devices are used in industry today, from turbines to generate rotational power to pumps and pistons to move gases and liquids. Axial pumps, meanwhile, are a particularly important piece of hardware that enable axial flow of materials. Any responsible factory owner will have an axial pump inspected or repaired every so often as needed, since disrupted axial flow could be a real problem. An agricultural water pump may use similar concepts, and industrial pump rental is also an option for those interested. To maintain proper axial flow, any pump should be the right model for the job, and it should be kept in fine working order. What is there to know about axial flow and these pumps?
On Axial Flow and Pumps
According to Engineering 360, axial flow pumps, sometimes known as propeller pumps, are a centrifugal model of pump that can move fluid axially through an impeller. Overall, these pumps make for high flow rates while in operation as well as low head, but certain models of these pumps can be adjusted. If adjusted, they may run efficiently under different conditions when the impeller’s pitch is adjusted.
These are dynamic pumps. That is, they make use of fluid momentum and velocity to generate their pump pressure during work. In particular, they are centrifuge pumps, and they generate this velocity by using their impeller hardware to apply centrifugal force to moving liquid. Axial flow pumps are, in fact, one of three different centrifugal pump sub-types, and of these three types, axial pumps have the highest flow rate, and the lowest discharge pressures. These pumps, during operation, will direct flow in a straight line parallel to the impeller shaft (as opposed to radially). This impeller is shaped like a propeller, and while in use, it makes use of its three or four vanes (depending on the model). A motor makes the impeller run, often with a drive shaft to keep the motor clear of the flowing liquids. Since these impellers visually resemble boat propellers, axial pumps are sometimes nicknames “propeller” pumps.
These pumps may be built out of different materials, which may alter how they function during work. Cast iron, for example, has high tensile strength and durability, and such pumps can resist high pressure ratings as a result. Plastics, meanwhile, are inexpensive to purchase and are highly resistant to chemical corrosion, which is an essential factor in some situations. A chemical plant, for example, may have great use for these plastic pumps, alongside metal pipes made from corrosion-resistant alloys. And finally, a third material for axial pumps is steel (or stainless steel alloys). These pumps are also resistant to chemical corrosion, and they have more tensile strength than plastics. This is useful if higher pressure ratings are to be expected during operations. Other materials, meanwhile, may include brass, ceramics, or even nickel-alloy.
When a factory or plant manager is deciding which model of axial pump to purchase and install, that manager may have to weigh some factors for best results. For example, a chemical plant is a place that deals with highly corrosive liquids, and not just any materials will do. Pumps, carrying tanks, valves, pipes, and more must be chemical-resistant, or frequent breakdowns will occur. A chemical plant manager may consult a metallurgist for this concern and determine which materials are best to use. Or, the pump may be used for moving edible materials such as soft drinks or dairy, and in this case, the pump must be absolutely leak-proof and also easy to clean and maintain for sanitation purposes.
The density of the liquids being moved is another factor, since thicker materials such as sludge need more power to move. Axial pumps, meanwhile, are better suited for thinner, low-viscosity fluids such as oil and water, which require less power to move. Finally, it should be noted that liquids with solids in them may damage or disrupt an axial pump, which are better suited for high-consistency materials.